9 Important Types of Insulation
Installing Insulation
There are many types of insulation. The optimal thermal performance or R-value of insulation is heavily influenced by correct installation. Certain, such as blankets, boards, and pour-in materials, can be installed by homeowners themselves. However, it’s important to note that liquid foam insulation materials require professional installation. Additionally, there is other that also necessitates professional installation.
When enlisting the services of a certified professional installer:
- Request written cost estimates from multiple contractors for the desired R-value, and be prepared for significant variations in quoted prices for installations with the same R-value.
- Inquire about contractors’ experience with the specific product you are considering, as the installation process can greatly influence the performance of the insulation.
- Discuss with contractors their air-sealing services and associated costs, as it is advisable to address air leaks prior to insulation installation.
To assess the installation of different types of insulation, such as blanket insulation, it is recommended to measure the thickness of the batts and check for gaps between the batts and framing. Additionally, inspect the insulation for a tight fit around building components that penetrate the insulation, such as electrical boxes. When evaluating sprayed or blown-in insulation, it is important to measure the depth of the insulation and check for any gaps in coverage.
If you choose to install different types of insulation yourself, following manufacturer’s instructions and safety precautions is crucial. It is also essential to consult local building and fire codes for compliance. Instructions for do-it-yourself installation can be obtained from trade groups associated with fiberglass and mineral wool insulation. While the cellulose trade group recommends hiring a professional, if there is a lack of qualified installers in your area or if you feel confident in undertaking the task, manufacturers may provide guidance to assist you.
1: Insulating Concrete Forms
Material:
- Foam boards or foam blocks
Where applicable:
- Unfinished walls, including foundation walls for new construction
- Installation methods: Installed as part of the building structure. Cores in the blocks are typically filled with concrete to create the structural component of the wall
Advantages:
- Insulation is literally built into the home’s walls, creating high thermal resistance.
Insulating concrete forms (ICFs) serve as molds or forms for poured concrete walls and remain in place as part of the wall assembly. This construction system creates walls with exceptional thermal resistance, typically achieving an R-value of about R-20. Interestingly, despite being built with concrete, ICF homes maintain the appearance of traditional stick-built homes.
ICF systems, among various types of insulation, consist of interconnected foam boards or interlocking hollow-core foam insulation blocks. The foam boards are securely fastened together using plastic ties, creating a rigid framework. In some cases, steel rods (rebar) can be incorporated for additional reinforcement before the concrete is poured. When using foam blocks, steel rods are often inserted into the hollow cores to strengthen the walls further.
When considering different types of insulation, it is important to note that the foam webbing surrounding the concrete-filled cores of the blocks can provide easy access for insects and groundwater. To mitigate these potential issues, some manufacturers offer insecticide-treated foam blocks and recommend specific waterproofing methods. Installing an ICF system, among various types of insulation, requires the expertise of an experienced contractor, who can be sourced through the Insulating Concrete Form Association. Their knowledge and skills ensure proper installation and maximize the benefits of the ICF system.
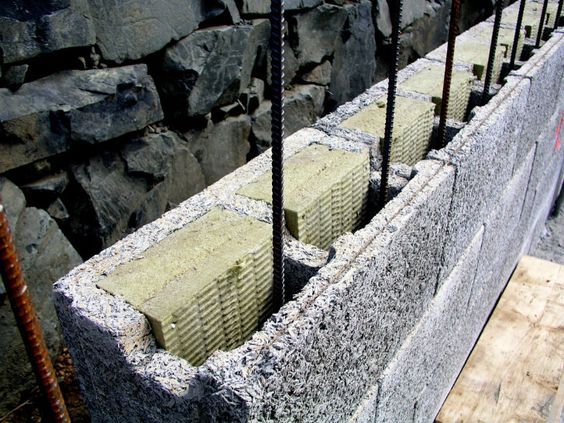
2: Foam Board or Rigid Foam
Material:
- Polystyrene
- Polyisocyanurate
- Polyurethane
- Phenolic
Where applicable:
- Unfinished walls, including foundation walls
- Floors and ceilings
- Unvented low-slope roofs
Installation methods:
- Interior applications: must be covered with 1/2-inch gypsum board or other building-code approved material for fire safety.
- Exterior applications: must be covered with weatherproof facing.
Advantages:
- High insulating value for relatively little thickness
- Can block thermal short circuits when installed continuously over frames or joists
Foam boards, among the various types of insulation, are rigid panels that offer versatile insulation options for various parts of your home, covering everything from the roof to the foundation. They prove particularly effective in exterior wall sheathing, interior sheathing for basement walls, and specialized applications like attic hatches.
These boards exhibit excellent thermal resistance, often surpassing other insulation materials of same thickness by up to two times. By reducing heat conduction through structural elements such as wood and steel studs, they enhance energy efficiency. The most commonly used materials in the production of foam boards include polystyrene, polyisocyanurate (polyiso), and polyurethane. These materials ensure reliable insulation performance and contribute to the overall thermal efficiency of your home.
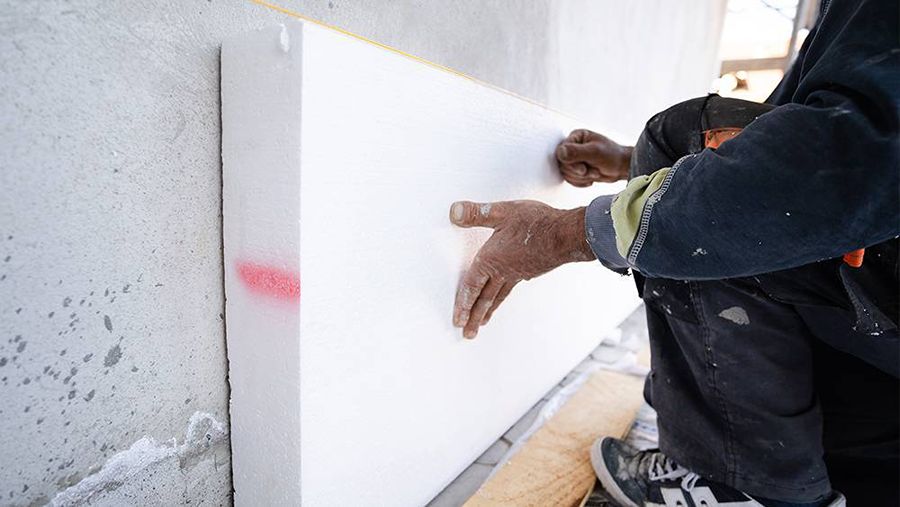
3: Concrete Block Insulation
Material:
- Foam board, to be placed on outside of wall (usually new construction) or inside of wall (existing homes):
- Some manufacturers incorporate foam beads or air into the concrete mix to increase R-values
Where applicable:
- Unfinished walls, including foundation walls
- New construction or major renovations
- Walls (insulating concrete blocks)
Installation methods:
- Require specialized skills
- Insulating concrete blocks are sometimes stacked without mortar (dry-stacked) and surface bonded
Advantages:
- Insulating cores increases wall R-value.
- Insulating outside of concrete block wall places mass inside conditioned space, which can moderate indoor temperatures
- Autoclaved aerated concrete and autoclaved cellular concrete masonry units have 10 times the insulating value of conventional concrete
It is also one of the types of insulation. Concrete blocks are commonly used for building home foundations and walls, and there are various methods to insulate them. If the cores of the blocks are not filled with steel and concrete for structural purposes, they can be filled with insulation to increase the overall wall R-value. However, research studies and computer simulations have indicated that core filling, regardless of the insulation type, offers minimal energy savings since heat can easily conduct through the solid sections of the walls.
A more effective approach is to install insulation on the surface of the blocks, either on the exterior or interior of the foundation walls. Exterior insulation offers an additional benefit of keeping the thermal mass of the blocks within the conditioned space, which can help regulate indoor temperatures.
Some manufacturers incorporate polystyrene beads into concrete blocks, while others design blocks that can accommodate rigid foam inserts for insulation purposes.
In the United States, there are now two types of solid, precast autoclaved concrete masonry units available: autoclaved aerated concrete (AAC) and autoclaved cellular concrete (ACC). These materials have been widely used in Europe since the late 1940s. Autoclaved concrete is unique in that it contains approximately 80% air by volume, giving it exceptional insulation properties compared to conventional concrete. The large size of the blocks, combined with their lightweight nature, allows for easy cutting, nailing, and shaping using standard tools. However, it is important to protect autoclaved concrete from moisture as it tends to absorb water readily.
Precast ACC sets itself apart from AAC by using fly ash instead of high-silica sand. Fly ash is a byproduct obtained from the combustion of coal in electric power plants. This substitution of materials provides distinct characteristics to ACC.
There are hollow-core units available that are made with a combination of concrete and wood chips. These units can be installed by stacking them without mortar, a method known as dry-stacking, and then filling the cores with concrete and structural steel. However, it’s important to note that this type of unit can be susceptible to moisture and insect damage due to the presence of wood.
When it comes to new home construction or significant renovations, concrete block walls are often insulated or constructed using insulating concrete blocks. In the case of existing homes with block walls, insulation can be added from the inside. If you’re interested in learning more about the insulation materials commonly used for concrete block, refer to the section on insulation materials for additional information.
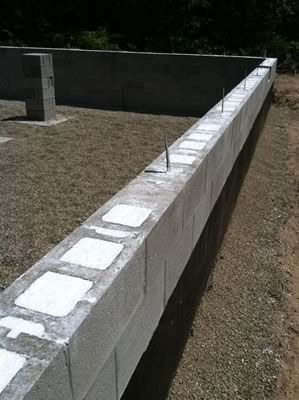
4: Blanket: Batts and Rolls Insulation
Material:
- Fiberglass
- Mineral (rock or slag) wool
- Plastic fibers
- Natural fibers
Where applicable:
- Unfinished walls, including foundation walls
- Floors and ceilings
Installation methods:
- Fitted between studs, joists, and beams
Advantages:
- Do-it-yourself
- Suited for standard stud and joist spacing that is relatively free from obstructions
- Relatively inexpensive
Blanket insulation, which is the most prevalent and easily accessible type of insulation among different types of insulation, is typically available in the form of batts or rolls. It is composed of flexible fibers, with fiberglass being the most commonly used material. Alternatively, you can also find batts and rolls made from mineral wool (derived from rocks and slag), plastic fibers, and natural fibers like cotton and sheep’s wool. Each of these insulation materials possesses distinct characteristics and properties that contribute to their thermal performance and suitability for specific applications. To gain a deeper understanding of these insulation materials, it is advisable to explore further information about their composition, benefits, and potential considerations.
Batts and rolls of insulation are designed to align with the standard spacing of wall studs, attic trusses or rafters, and floor joists. They come in various widths to accommodate different wall sizes: for 2 inch x 4 inch walls, R-13 or R-15 batts are suitable, while 2 inch x 6 inch walls can accommodate R-19 or R-21 products. Continuous rolls can be easily cut and trimmed by hand to fit specific dimensions. These insulation materials are available with or without facings, which are attached by manufacturers. Facings, such as kraft paper, foil-kraft paper, or vinyl, serve multiple functions including acting as vapor barriers and/or air barriers. Additionally, among different types of insulation, there are batts with special flame-resistant facings that come in various widths, intended for use in basement walls and other areas where the insulation will be left exposed. The presence of a facing also aids in handling and fastening during the installation process.
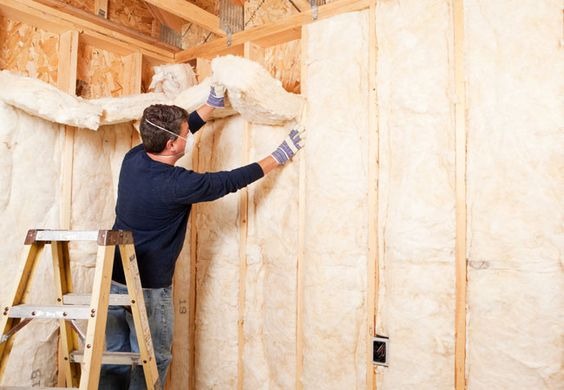
5: Loose-Fill and Blown-In
Material:
- Cellulose
- Fiberglass
- Mineral (rock or slag) wool
Where applicable:
- Enclosed existing wall or open new wall cavities
- Unfinished attic floors
- Other hard-to-reach places
Installation methods:
- Blown into place using special equipment and, although not recommended, sometimes poured in
Advantages:
- Good for adding insulation to existing finished areas, irregularly shaped areas, and around obstructions
Loose-fill insulation is made up of small fiber, foam, or other material particles. It can easily conform to any space without causing disruptions to structures or finishes. This flexibility makes it ideal for retrofits and challenging installation areas where other insulation types may be impractical.
The most frequently used materials for loose-fill insulation are cellulose, fiberglass, and mineral wool, which are all made from recycled waste materials. Cellulose is derived from recycled newsprint, while fiberglass contains a significant amount of recycled glass (40% to 60%). Mineral wool is primarily produced from 75% post-industrial recycled content.
In addition to these common materials, there are some less commonly used loose-fill insulation options, such as polystyrene beads and perlite. Loose-fill insulation can be installed in enclosed cavities like walls or in unenclosed spaces like attics. Cellulose, fiberglass, and rock wool are typically blown into place by experienced installers who ensure proper density and achieve the desired R-values. On the other hand, polystyrene beads, vermiculite, and perlite are commonly poured into the designated areas.
The Federal Trade Commission (FTC) has established a rule known as the “Trade Regulation Rule Concerning the Labeling and Advertising of Home Insulation” (16 CFR Part 460). This rule aims to prevent unfair or deceptive practices in the industry. It requires manufacturers and sellers of home insulation to disclose the R-value and related information of their products on package labels and fact sheets. The R-value indicates the insulation’s effectiveness, and it varies depending on the type and form of insulation.
For loose-fill insulation, each manufacturer is responsible for determining the R-value at settled density. They must also provide coverage charts that specify the minimum settled thickness, minimum weight per square foot, and coverage area per bag for different total R-values.
The settled density of loose-fill insulation increases as its installed thickness increases due to compression. Consequently, the R-value does not change proportionally with thickness. The manufacturers’ coverage charts detail the number of bags required per square foot of coverage, the maximum coverage area per bag, the minimum weight of the installed insulation per square foot, and the initial and settled thickness needed to achieve a specific R-value.
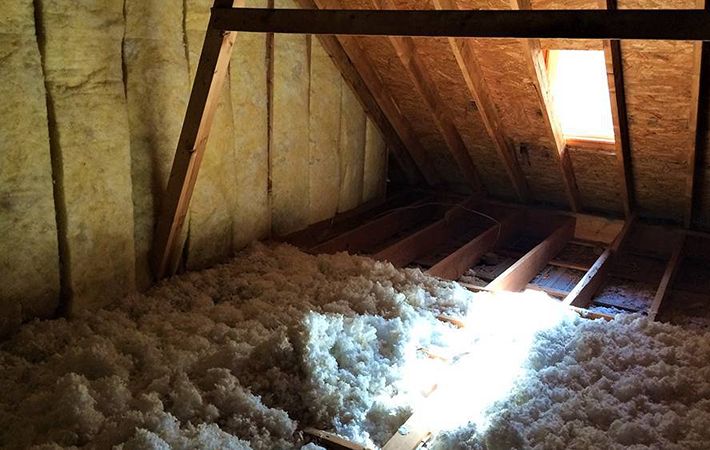
6: Reflective Insulation Systems
Material:
- Foil-faced kraft paper, plastic film, polyethylene bubbles, or cardboard
Where applicable:
- Unfinished walls, ceilings, and floors
Installation methods:
- Foils, films, or papers fitted between wood-frame studs. Joists, rafters, and besms.
Advantages:
- Do-it-yourself
- Suitable for framing at standard spacing
- Bubble-form suitable if framing is irregular or if obstructions are present
- Most effective at preventing downward heat flow, effectiveness depends on spacing and number of foils
Unlike conventional insulation systems that primarily resist conductive and convective heat flow, radiant barriers and reflective insulation function by reflecting radiant heat. Radiant barriers are commonly installed in homes, typically in attics, with the main purpose of reducing summer heat gain, thus lowering cooling costs. Reflective insulation, on the other hand, incorporates reflective surfaces, usually made of aluminum foils, into insulation systems that may include various backings such as kraft paper, plastic film, polyethylene bubbles, cardboard, and thermal insulation materials.
Radiant heat moves in a straight line away from any surface and heats any solid material that absorbs its energy. When the sun’s radiant energy warms a roof, it is primarily this radiant heat that increases the roof’s temperature. A significant portion of this heat is then conducted through the roofing materials to the attic side of the roof. From there, the hot roof material radiates its accumulated heat energy onto cooler surfaces within the attic, including air ducts and the attic floor. A radiant barrier diminishes the transfer of radiant heat from the underside of the roof to other surfaces in the attic, provided it faces a substantial air space.
Radiant barriers are most effective in hot climates, particularly when cooling air ducts are situated in the attic. Some studies indicate that using radiant barriers in warm, sunny climates can reduce cooling costs by 5% to 10%. Furthermore, the decreased heat gain may even allow for the use of a smaller air conditioning system. However, in cooler climates, it is generally more cost-effective to focus on installing additional thermal insulation to improve energy efficiency.
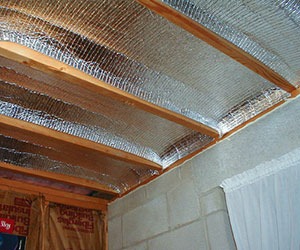
7: Rigid Fiber Board Insulation
Material:
- Fiberglass
- Mineral (rock or slag) wool
Where applicable:
- Ducts in unconditioned spaces
- Other places requiring insulation that can withstand high temperatures
Installation methods:
- HVAC contractors fabricate the insulation into ducts either at their shops or at the job sites.
Advantages:
- Can withstand high temperatures
Rigid fiber or fibrous board insulation, made of fiberglass or mineral wool material, serves as an excellent choice for insulating air ducts in residential buildings. Its durability and ability to withstand high temperatures make it particularly suitable for such applications. These insulation products are available in various thicknesses, ranging from 1 inch to 2.5 inches.
Installation of rigid fiber or fibrous board insulation in air ducts is typically carried out by HVAC contractors. They fabricate the insulation either at their workshops or directly at the job sites. When applying the insulation to the exterior surfaces of ducts, they secure it by impaling it on weld pins and fastening it with speed clips or washers. Alternatively, special weld pins with integral-cupped head washers can be used. Unfaced boards can be further enhanced by applying reinforced insulating cement, canvas, or weatherproof mastic. Faced boards can be installed using the same methods, and the joints between boards can be sealed using pressure-sensitive tape or glass fabric and mastic to ensure proper insulation coverage and performance.
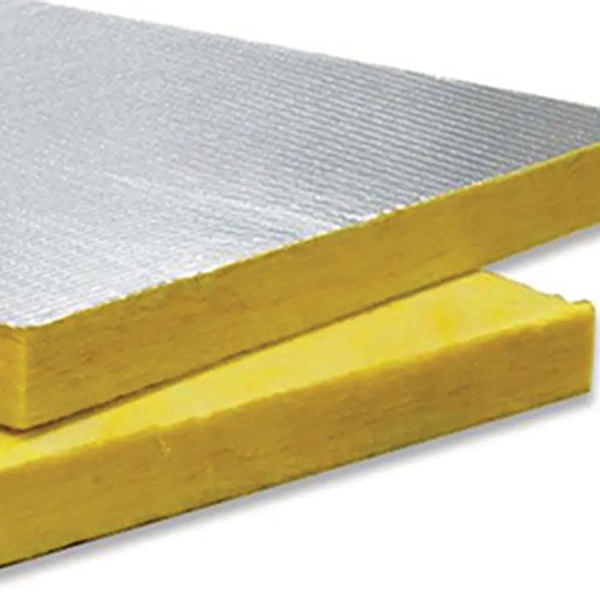
8: Sprayed-Foam and Foamed-In-Place Insulation
Material:
- Cementitious
- Phenolic
- Polyisocyanurate
- Polyurethane
Where applicable:
- Enclosed existing wall
- Open new wall cavities
- Unfinished attic floors
Installation methods:
- Applied using small spray containers or in larger quantities as a pressure sprayed (foamed-in-place) product.
Advantages:
- Good for adding insulation to existing finished areas, irregularly shaped areas, and around obstructions.
Liquid foam insulation materials offer versatile options for insulating buildings and can be applied through spraying, foaming-in-place, injection, or pouring. Foam-in-place insulation is particularly beneficial as it can be blown into walls, applied on attic surfaces, or placed under floors to effectively insulate and minimize air leakage. Compared to traditional batt insulation of the same thickness, certain foam-in-place installations can provide a higher R-value, making them more efficient in reducing heat transfer. Additionally, the foam’s ability to expand allows it to fill even the tiniest cavities, creating a robust air barrier that enhances overall insulation performance. For smaller areas requiring insulation and air sealing, such as window and door frames, as well as electrical and plumbing penetrations, pressurized cans of foam-in-place insulation can be used to effectively reduce air leakage and improve energy efficiency.
Types of Foam Insulation
In modern times, foam materials predominantly utilize foaming agents that are free from chlorofluorocarbons (CFCs) or hydrochlorofluorocarbons (HCFCs), which are known to harm the Earth’s ozone layer.
Foam-in-place insulation comes in two types: closed-cell and open-cell, both typically made with polyurethane. Closed-cell foam consists of densely packed cells that are sealed and filled with gas, allowing the foam to expand and fill surrounding spaces. On the other hand, open-cell foam has less dense cells filled with air, resulting in a softer, spongy texture.
The choice of insulation depends on its intended use and your budget. Closed-cell foam offers a higher R-value and superior resistance against moisture and air leakage, but it is also denser and more costly. Open-cell foam, while lighter and less expensive, should not be used below ground level as it has the potential to absorb water. It is advisable to consult a professional insulation installer to determine the most suitable type of insulation for your needs.
Other Available Foam Insulation Materials
- Cementitious
- Phenolic
- Polyisocyanurate (polyiso)
There are a few lesser-known types of foam insulation, such as Icynene foam and Tripolymer foam. Icynene foam offers exceptional versatility as it can be either sprayed or injected. Additionally, it provides effective resistance against both air and water infiltration. On the other hand, Tripolymer foam, which is water-soluble, is injected into wall cavities. This type of foam demonstrates excellent resistance to fire and air infiltration.
Installation
Liquid foam insulation, when combined with a foaming agent, offers versatile application methods. It can be applied using small spray containers or as a larger, pressure-sprayed (foamed-in-place) product. Both types of application result in expansion and hardening as the mixture cures, effectively filling and sealing the cavity.
For specific needs, there are slow-curing liquid foams available. These foams are designed to flow over obstructions before expanding and curing, making them suitable for empty wall cavities in existing buildings. Additionally, certain liquid foam materials can be poured from a container.
It’s important to note that the installation of most liquid foam insulation requires specialized equipment and certification, and it should be carried out by experienced installers. After installation, all foam materials must be covered by an approved thermal barrier that provides the same level of fire resistance as half-inch gypsum board. It’s worth mentioning that some building codes do not recognize sprayed foam insulation as a vapor barrier, so an additional vapor retarder may be necessary during installation.
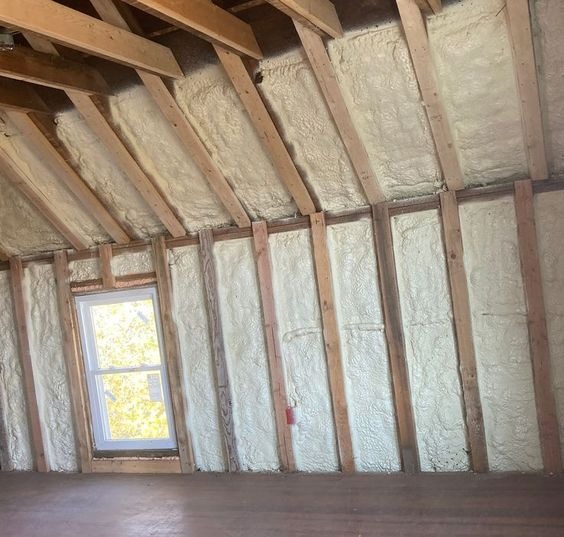
9: Structural Insulated Panels
Material:
- Foam board or liquid foam insulation core
- Straw core insulation
Where applicable:
- Unfinished walls, ceilings, floors, and roofs for new construction
Installation methods:
- Construction workers fit SIPs together to form walls and roof of a house
Advantages:
- SIP-built houses provide superior and uniform insulation compared to more traditional construction methods; they also take less time to build.
Structural insulated panels (SIPs) are pre-made structural components designed for use in constructing walls, ceilings, floors, and roofs. They offer superior and consistent insulation compared to traditional construction methods like stud framing, resulting in energy savings of 12% to 14%. Proper installation of SIPs also leads to a more airtight building, enhancing energy efficiency, noise reduction, and overall comfort.
SIPs possess both high R-values and impressive strength-to-weight ratios. Typically, a SIP consists of insulation foam board, ranging from 4 to 8 inches in thickness, sandwiched between two sheets of oriented strand board (OSB) or other structural facing materials. Manufacturers can customize the sheathing materials to meet specific requirements. The facing is securely bonded to the foam core through gluing and pressing, sometimes with the aid of vacuum technology.
SIPs come in various sizes or dimensions, with some panels measuring as large as 8 by 24 feet, necessitating the use of a crane during installation.
The quality of SIP manufacturing greatly influences the product’s longevity and performance. Proper gluing, pressing, and curing processes are crucial to prevent delamination. Additionally, the panels should have smooth surfaces and square edges to ensure seamless connections at the construction site. Before purchasing SIPs, it is important to inquire about manufacturers’ quality control and testing procedures, and carefully review and compare warranties. SIPs are available with different insulation materials, typically polystyrene or polyisocyanurate foam.
Installation:
SIPs are prefabricated in a factory and then transported to the construction site, where they are assembled by builders to create a house. Compared to traditional construction methods, experienced builders can erect a SIPs home much faster, resulting in time and cost savings without compromising quality. These savings can help offset the typically higher initial cost of SIPs.
In addition to fully assembled SIPs, many manufacturers also offer “panelized housing kits.” These kits include pre-cut pieces that the builder simply needs to assemble, and standard tools can be used to create openings for doors and windows at the construction site.
When SIPs are installed in accordance with the recommendations of the manufacturers, they meet all building codes and adhere to the safety standards set by the American Society for Testing and Materials (ASTM). This ensures that SIPs provide a safe and compliant construction solution.
Areas of Concern:
Ensuring fire safety is an important consideration when using SIPs. However, when the interior of the SIP is covered with a fire-rated material like gypsum board, it provides protection to the facing and foam, offering occupants sufficient time to evacuate in case of a fire emergency.
Just like in any other house, insects and rodents can pose a potential issue. In rare instances, these pests have burrowed through SIPs. To address this concern, certain manufacturers have provided guidelines to prevent such problems, including:
- Implementing insecticide application on the panels
- Administering ground treatment with insecticides prior to and after initial construction and backfilling
- Sustaining indoor humidity levels below 50%
- Placing outdoor plantings at least two feet (0.6 meters) away from the walls
- Pruning any tree limbs that extend beyond the walls
Insulation panels treated with boric acid are an option to deter insects while posing minimal risk to humans and pets.
Due to its high level of airtightness, a properly constructed SIP structure may necessitate controlled ventilation to ensure safety, health, and optimal performance in compliance with building codes. Implementing a well-designed, correctly installed, and effectively operated mechanical ventilation system can also help mitigate indoor moisture issues, which is crucial for maximizing the energy-saving advantages of a SIP structure.
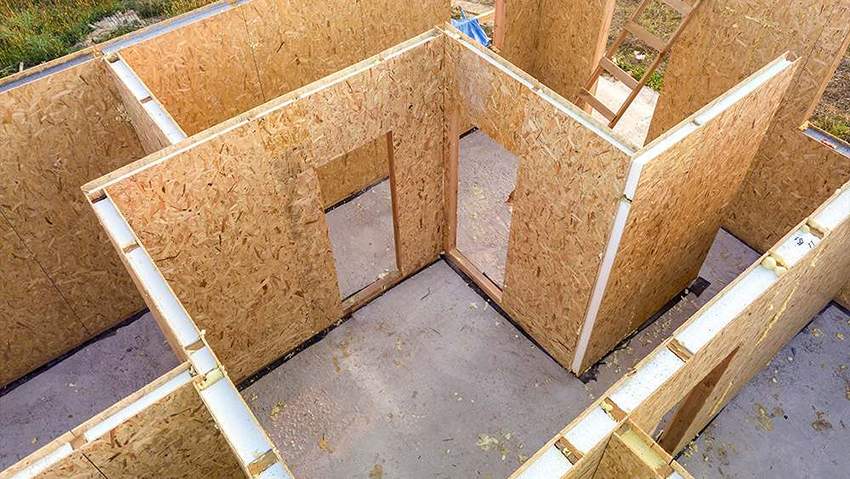